Pulping Process
Woodchips from trees and saw mills get transported via truck or sometimes conveyor belt to a pulp mill alongside de-inked recycled paper and other plant fibres. A pulp mill breaks down the bulk structure of raw materials then separates the wood fibres and other fibres to turn it into a thick fibrous board. This board can be transported to a paper-mill. A paper mill turns the board into the final product.
Recycled pulp:
Recycled pulp is also commonly known as de-inked pulp. It is recycled paper which has had the ink and other materials removed by a chemical process to extract the paper fibres. This gets mixed in with the pulp that gets transported to the paper mill.
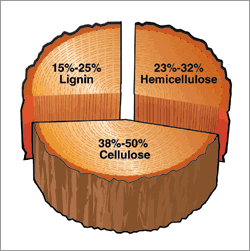
There are numerous processes that can breakdown the lignin within the wood cell walls to separate the wood fibre. Such as:
-
Mechanical Pulping
-
Thermomechanical Pulping
-
Chemi- Thermomechanical Pulping
-
Chemical pulping
-
Organosolv pulping

Mechanical pulping:
In mechanical pulping stations, such as the Iggesund Paperboard (Iggesund Paperboard AB, 2008) pulping station, mechanical pulping is most common. This is where wood chips are ground using metal refiner disks. The heat and water vapour generated soften the lignin so the fibres can be separated. It provides a low quality product relatively cheaply. Is mainly for papers and cardboards that require less refinement. Adding heat or steam to this process turns it into a thermomechanical pulping process (Bura, R, 2010).

Thermomechanical pulping:
In New Zealand pulping stations such as Pan Pac (Pan Pac, 2014) and in Finnish pulping stations such as Metso (Metso, 2011), Thermomechanical Pulping is very similar to Mechanical Pulping except the process chips are initially fed into a pre-steamer and the wood chips involved have a much higher moisture rate. These wood chips are then fed into a mechanical refiner. The steam softens the lignin and allows the fibres to be separated more easily.
Chemi-Thermomechanical pulping:
Chemi-Thermomechanical pulping is relatively similar to Thermomechanical pulping except the woodchips are pre-treated with chemicals such as sodium carbonate, sodium hydroxide, sodium sulfite and other chemicals (Qinyang Haiyang Paper Machinery, 2014).
Chemical Pulping:
Sappi (2012) in North America and CHH Pulp and Paper (2015) in New Zealand use Chemical Pulping to turn wood into wood pulp consisting of almost pure cellulose fibres. Chemical Pulping is often referred to as the Kraft or Sulfate process or Kraft Pulping. Unlike Mechanical pulping, Chemical Pulping mainly focuses on extracting the lignin completely turning it into almost pure cellulose fibres to make the pulp. The wood chips go into a pressure vessel called a digester where it is refined chemically. The chemicals used are a range of sulfurous acids similar to the Chemi-Thermomechanical process except at a lower pH/stronger acid, higher temperature and for longer.
Organosolv pulping:
Currently there are no Organosolv Pulping stations in New Zealand. However this process has a few advantages over Chemical Pulping such as less water pollution and less odour. It uses high temperatures and organic solvents such as methanol, ethanol, formic acid and acetic acid to break down the lignin and hemicellulose of the chips the chemicals are better for this makes for high quality lignin extracts and less waste as it can be easily recovered with distillation. (Schwiderski & Kruse, 2015)
The pulp from these processes are washed and bleached and filtered so it doesn't yellow. Oxygen and peroxide is used to bleach it to reduce harm on the environment. This pulp this pulp is then dried and bundled to go to other paper mills.
The pulp enters the paper mill and is mixed with water. It is refined by passing through blades, this can control the thickness, texture and strength of the paper. Calcium carbonate, clay, dyes and optical brighteners are added to change the density and appearance of the paper.
About 100 litres of fresh water is needed to make one kilogram of paper. In some pulp mills they use waste water treatment plants and closed water circulation systems allow 90% of the water to be recycled.
The pulp solution is the ideal mix of fibres and colouring agents suspended in water. The paper machine to convert the pulp solution. The head box. In this the pulp solution has the water removed and it can it gets turned into a continuous web of paper ready for further processing.