Pulp Injection Moulding
My topic to further development was “hard plastics”, hard plastics is something that is currently heavily dependent on petroleum and is unsustainable at the current rate of usage. So it could potentially have a good market if a sustainable paper product could have the same function. My goal was to design a process for which paper could be used to replace injection moulded plastic.
-
Paper slurry is gravity fed into an auger and forced into a mould. The inner mould being a solid form and the outer a permeable surface to allow the moisture content to be extracted under the pressure applied from the auger.
-
Moisture would then be drained from the system leaving a strong, biodegradable fibrous formed product.
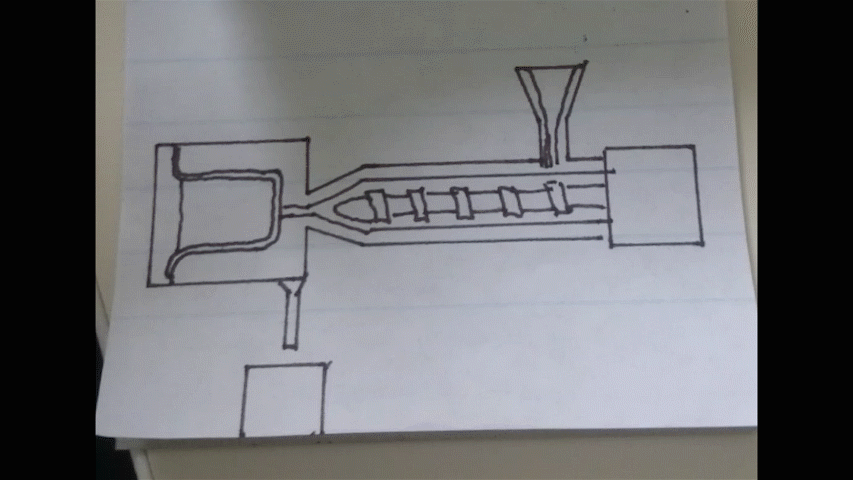
The injection moulding process would work like the traditional plastic injection moulding. Paper slurry would be gravity feed from a hopper into an auger and forced into a mould (see fig 1). The mould however would be completely re-designed with the inner half of the mould being a solid form and the outer a permeable surface to allow the moisture content to be extracted under the pressure applied from the auger (see fig 2). Moisture would then be drained from the system leaving a strong dry fibrous formed product. This process could be developed as a retrofit to existing plastic injection moulding systems for a more environment friendly product. The auger would be driven by an electric motor and force the paper slurry at such a pressure that all moisture content is removed. The end plug mould could be driven by an external hydraulic ram to hold the mould in place during the process and then release the product when finished. The process and products could be scaled up or down depending on the application.

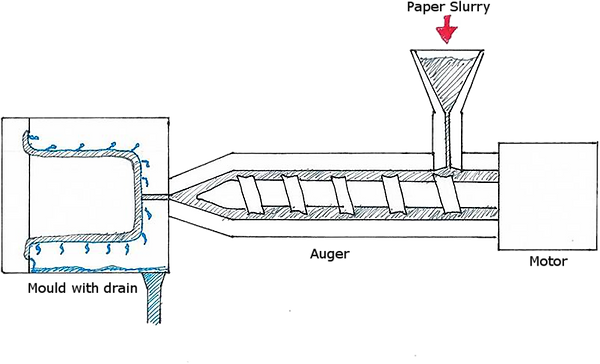
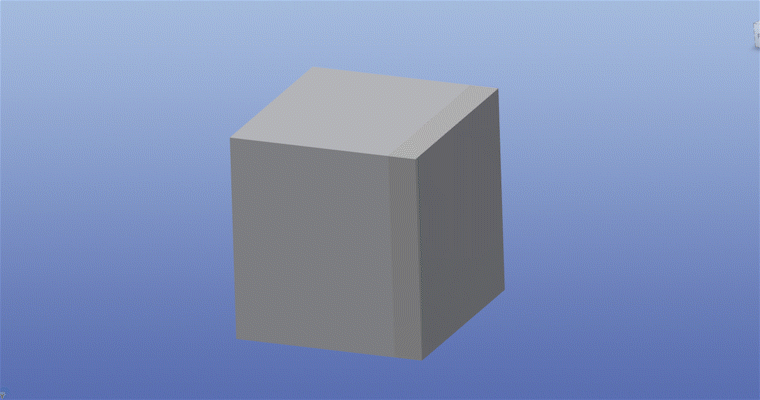
Timeline 2015 - 2070
Research stage: 2015 – 2030 For this product/process to be successful it needs to be working perfectly and have all safety/health standards met. It is vital that the necessary research is done to ensure this. A range of porotypes products should be made to showcase this sustainable technology. It would also be beneficial to have a range of different paper slurry products available such as waterproof, biodegradable and fire retardant. Products would undergo patent registration during this stage.
Product industry testing: 2025 – 2040
The start of releasing products and retrofit systems between the years 2025 – 2040 would give our paper industry some return on their investment and a chance for the products to been seen and tested by consumers. By the year 2030 some inflation of oil prices are likely meaning alternatives to plastic should be in demand. This could also be a chance for external investment into development
Marketing products and continuous improvement: 2035 - 2045
By the year 2035 our new products should be proven and reliable meaning we can push sales and continue to develop the new industry of paper injection moulding as the plastic industry petroleum based plastic industry weakens though price inflation.
Industry development: 2045 - 2069
By the year 2045 we should have improved our processes to the point where we have reliable industry solutions. We can continue to push these solutions to develop the industry worldwide.
The year 2070:
The year 2070 paper products like writing paper and other printed media will be almost in no demand, packaging should still make up a good proportion of the industry. Now paper injection moulding can also play a major part in the paper industry to keep it alive.